How do you get aluminum brass? How to make aluminum brass?
Aluminum brass has high strength
The corrosion resistance is the best among all brasses, the tendency of corrosion cracking is not big, the plasticity is low in a cold state, and the pressure workability is good in a hot state. Aluminum brass can be divided into two categories:
- add a small amount of aluminum to cast brass to remove impurities and increase fluidity. For complex castings, the amount of excess aluminum in the alloy does not exceed 0.5%.
- add aluminum to forged brass to increase the corrosion resistance. It is often used as a condenser. The general composition range is Al1-6%, Zn24-42%, and Cu55-71%.
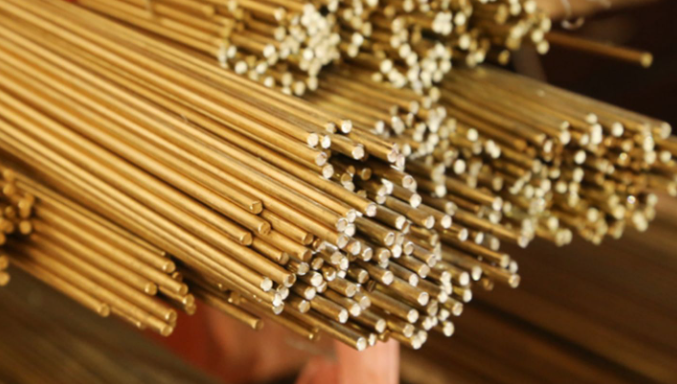
There are not many grades and types of aluminum brass. There are 6 grades of aluminum brass in the national standard.
The main elements are manganese, iron, and other elements added to aluminum brass to improve the alloy's comprehensive properties such as strength and wear resistance.
The more common aluminum brasses mainly include:
HAl77-2, HAl66-6-3-2, HAl64-3-1, and others HAl60-10-1, HAl59-3-2, etc.(C86400 Turbine Bearing)
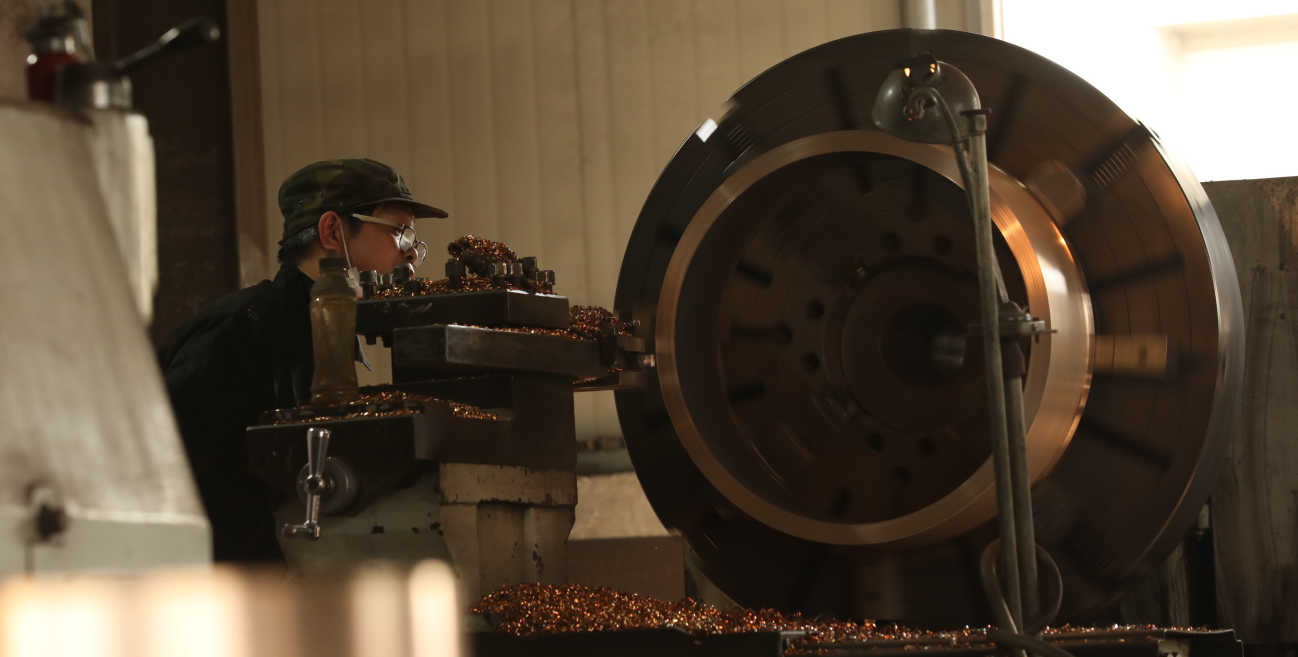
Basic Information:
- Ingredients: Electrolytic copper, pure aluminum, electrolytic manganese, electrolytic zinc, tinplate, high-purity microalloying elements. All ingredients are required to be free of oil, water, and impurities. The order of addition is determined by the solubility characteristics of Mn and Fe in brass.
- Equipment: Use a power frequency cored induction furnace for smelting. Because this furnace relies on the material itself to generate eddy current heating, it has the characteristics of fast melting speed, low working environment temperature, uniform copper temperature, and strong electromagnetic stirring force, so that it is easy to make the material composition uniform and easy to control the chemical composition of the material.
- Smelting: In order to save costs and improve production efficiency, the method of directly adding elements is adopted for smelting, which is difficult to melt.
|
GB/T |
BSEN |
Hardness |
Tensile Strength |
Ductility |
Max Load |
C86300 |
ZCuZn25Al6Fe3Mn3 |
CC762S |
180-240HB |
725-850Mpa |
>7% |
100N/mm² |
C86400 |
ZCuZn35Al2Fe2Mn2 |
CC765S |
120-150HB |
>475Mpa |
>18% |
100N/mm² |
After the Fe is melted, the remaining copper is added for cooling treatment, then zinc and aluminum are added to melt, the temperature is raised, tin and rare earth are added, stirred, and the temperature is sprayed out of the furnace for semi-continuous casting.
The smelting process is as follows:
- add electrolytic copper to the furnace,
- add a dry covering agent at the beginning of melting,
- add a deoxidizer after all melting, and each time it is fully covered, heat up to 1300°C,
- add Mn, and then add Fe after Mn is melted.
Pipe up with your ideas to our bearing specialist. Contact now!